Episodes
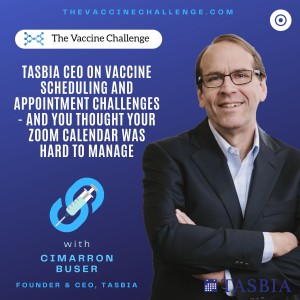
Thursday Apr 01, 2021
TASBIA CEO on Vaccine Scheduling & Appointment Challenges in USA
Thursday Apr 01, 2021
Thursday Apr 01, 2021
This episode of The Vaccine Challenge is hosted by Priyanka Asera and features Cimarron Buser, Founder and CEO of The Appointment Scheduling & Booking Industry Association (TASBIA). Cimarron is an industry expert, and represents providers of appointment scheduling solutions. He appreciates the value--and the challenges--of using technology to help individuals schedule Covid-19 vaccination appointments.
Have you ever thought about how the scheduling works if you’re a citizen looking to book a spot? Have you thought about the various challenges and bottlenecks if scheduling is done incorrectly? Imagine what happens when everything else is done right - in terms of demand planning and the logistics and the vaccines get to the clinics as they should, but eventually are not received by the beneficiaries because of scheduling gone wrong.
Add to this, is the additional complication that every state in the US follows their own rules and their own platforms and does not have a centralized database like the UK or Canada. How do you keep track then of your citizens getting inoculated and scheduling them back for the second doze? We discuss all this and more with Cimmaron.
Topics touched upon:
- Please take us through your journey of The Appointment Scheduling & Booking Industry Association (TASBIA) and how it is impacting the Vaccination effort in the United States
- What are some existing government efforts to solve the scheduling crisis and are they effective?
- What are some private and tech enabled initiatives to help solve scheduling?
- Facebook and Google recently got into the vaccine scheduling, can you please walk our listeners through how that effort is planning out?
- Inside the US, which states have used the scheduling infrastructure in the most effective way and which ones are facing hurdles?
- What about scheduling for CPR tests? Has that been streamlined since it’s more commonplace now?
- Are there lessons to be learnt in the scheduling industry from other countries?
- What have been the biggest takeaways for the industry and what changes would you like to see in the industry once we get past the pandemic?
- Ending on a hopeful note, by when do you think we will be done with the vaccine distribution?
About Cimarron
Cimarron Buser, Founder and CEO of The Appointment Scheduling & Booking Industry Association (TASBIA). Cimarron is an industry expert, and represents providers of appointment scheduling solutions. He appreciates the value--and the challenges--of using technology to help individuals schedule Covid-19 vaccination appointments.
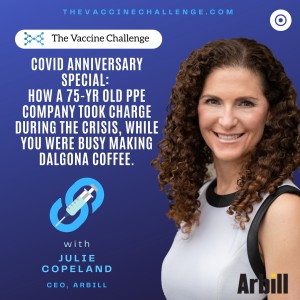
Friday Mar 26, 2021
Friday Mar 26, 2021
This episode of The Vaccine Challenge is hosted by Priyanka Asera and features Julie Copeland, CEO of Arbill. Arbill, a women-owned company that has been protecting workers for 75 years, focuses on saving lives every day through an array of PPE products including: hand protection, eye protection, hearing protection, head protection, respiratory protection, disposable clothing and independently-tested cloth face masks.
So when the pandemic hit in 2020 - they were right in the eye of the storm, and in a unique position to use their decades of expertise to jump in and take charge of the situation. And boy, did they deliver!
If you’ve thought about what goes down behind the scenes of a PPE company when they realize that this year is going to be very, very different, or how the demand for PPE has changed within industries in the last year, or indeed how an organization and its people step up and deliver when faced with a once-in-a-lifetime opportunity to really make a difference during a challenging phase -- listen on!
Topics touched upon:
-
We’re nearing the one year anniversary of the global lockdown. Since Arbill has been in the PPE business for over 75 years, describe that exact day or moment or incident last year when it clicked to you for the first time that PPE demand is going to be through the roof because of this new virus that’s taking over the world?
-
How did you as an organization step up to the challenge given you were in the eye of the storm and truly in a position to make a difference - but only at the cost of insane number of working hours
-
What were some of the initial challenges for Arbill back in Feb/March 2020 when things were unfolding at such a quick pace? What are the current challenges in comparison now that we’ve somewhat settled into the pandemic?
-
I remember when I tried to buy an N95 mask for the first time back in 2020 when I had to travel, I had no way to know which was good quality and which wasn’t. How does navigate the world of potential counterfeiting but also striking that balance between what is enough for a particular job and what might be overkill and therefore not necessary?
-
Can you quantify how the demand for PPE has changed from Pre-COVID to now? Which industries have become the highest adopters or users of it?
-
“PPE” and “face masks” have now become part of our normal lexicon. What else have you seen change as the result of the pandemic and what changes are here to stay?
-
What’s the biggest takeaway for you as a company from this pandemic?
About Julie
Julie Copeland has served as CEO of Philadelphia-based Arbill since 2005. Arbill, a women-owned company that has been protecting workers for 75 years, focuses on saving lives every day through an array of PPE products including: hand protection, eye protection, hearing protection, head protection, respiratory protection, disposable clothing and independently-tested cloth face masks. In 2015, Arbill became a GSA-approved provider of safety products to government agencies.
In her time as CEO, Copeland has led the Arbill team in producing nearly 1,000 safety-related Truline products, as well as launching SafetyCare – a full-service approach to all things safety. Arbill’s manufacturing operations have expanded to locations in eleven countries under Copeland’s leadership.
In 2020, as a result of the COVID-19 pandemic, Copeland launched a consumer division as a way to implement all that Arbill has learned in the past 75 years from working with enterprises, in order to efficiently protect everyday people. The first product in Arbill’s consumer line, the “Together: The Safety Mask,” was independently tested to European’s AFNOR standard and found to have 95% effective fabric filtration, inhibit microbial growth in fabric, be more breathable than disposable medical masks and maintain effectiveness up to 50 washes. Since developing The Safety Mask, Copeland has taken the lead on educating the public about proper cloth face coverings, sustainability in masks and things everyone should know when it comes to purchasing effective PPE.
In addition to striving to make the world a better and safer place, Copeland dedicates her time to give back to her community and serves as a board member for The American Red Cross in five counties throughout Southeastern Pennsylvania. Copeland has been recognized as one of Pennsylvania's Best 50 Women in Business, one of Enterprising Women’s Top Women Entrepreneurs and a Top 100 Visionary Leaders by Real Leaders Magazine. She also serves on the board of the National Association of Manufacturers, representing every U.S. industrial sector, and served as past Chair of the WBENC Forum leading 14,000 certified women-owned businesses for six years.
Copeland earned a bachelor’s degree in Communications from the S.I. Newhouse School of Communications at Syracuse University and master’s degree in Business Administration from Temple University. She has also participated in Harvard Business School’s Executive Program and the J.L. Kellogg Graduate School of Management at Northwestern University’s Innovation Program.
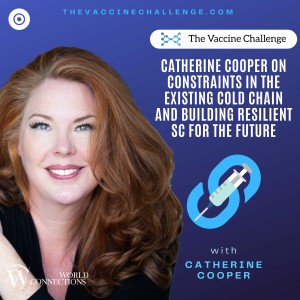
Thursday Mar 18, 2021
Thursday Mar 18, 2021
This episode of The Vaccine Challenge is hosted by Priyanka Asera and features Catherine Cooper, President & CEO of World Connections. Catherine has been in the logistics industry for two decades and has served various leadership positions. She now helps Fortune 500 companies to build resilient supply chains, and sits at the intersection of technology and people.
2020 was all about the pandemic. 2021 is all about the COVID-19 vaccines.
But what is the focus on vaccines doing to the overall cold chain capacity? What effect will the pandemic have on how boardrooms think about the need for resilient supply chains in the future? We discuss both of these crucial questions here.
Topics touched upon:
What is the magnitude of the impact the pandemic has had on supply chains globally?
- Economic global growth in 2019 was 2% and around that for previous years. The ‘economist intelligence unit’ is forecasting global economic growth this year at 4.2 % and that is on the back of a 4.7% contraction last year. We are having to manage a huge swing!
- Impact: Global trade and supply chains are being reshaped
- Countries are striving to diversify their export markets and capture redirected manufacture investment
- Companies concurrently are seeking to diversify their supply chains
- Additionally, people could see risks that were not directly related to but many clearly exacerbated by Covid -19
What is the definition of supply chain resilience and how does one work on achieving it
- Definition of Supply chain Resilience - the ability to quickly adjust to sudden, unexpected disruptive changes that can negatively affect supply chain performance
- How can supply chain resiliency be built in:
- Supply chain resilience can be strengthened by increasing inventory levels of raw material, work-in-progress, and the final product; adding manufacturing and/or storage capacity to improve manufacturing surge capability; and increasing the number of key suppliers and ensure their economic stability, surge capability, and geographical distribution
- End-to-end, data-driven, supply chain control. Supply chain integration, transparency, and visibility are necessary but not sufficient conditions for enhanced resilience. Being able to view raw materials, semi-finished goods, and finished products starting from your “suppliers’ suppliers” to your “customers’ customers” is more important than ever
- Build in redundancy: Redundancies, including emergency stockpiles, safety stocks, and diversified sourcing suppliers. These suppliers must be able to provide additional surge capacity when there are disruptions of supply to ensure business continuity.
- Near-shoring at least some capacity and supplier base
What incidents led to such added pressure on the existing cold chain?
On Nov. 9, Pfizer made history by announcing that their coronavirus vaccine had an efficacy rate of over 90 percent.
Cascading consequences that led to such complexities:
-
- Pandemic lockdown, people stop traveling. Gasoline and jet fuel is based on customer demand. With the lockdowns demand for gas dropped by 28% and jet fuel by 70%
- In June we started seeing widespread ethanol plant shutdowns – those plants produce CO2 by-product and provide 45% of the domestic CO2
- This resulted in limited dry ice
- Then layer on top Pfizer demand
- This resulted in a huge crisis
- Then in Q3 to Q4, the demand for dry ice went up 700% and ultracold freezers by over 800%. One solution was to increase inventory but dry ice can’t be stockpiled.
- Ramifications of ULT Vaccines requiring -80F
- Freezer capacity, dry ice, co2, chemical, shipping containers
- Temperature excursion parameters (maintaining these very tight brackets was not of mass concern before)– what is the range and how long can it be out of range before it goes bad
- No freezer capacity in many regions as a result
- 3PLs entered to help the situation. FedEx and UPS invested in dry ice manufacturing at their respective hubs. UPS says it can produce 24,000 pounds of dry ice per day
What SC changes will stay post pandemic and how are board rooms talking about this?
- Ecom – pulled forward 5-20 years due to forced acceleration, forced experimentation and forced adoption
- Grocery Online sales have doubled in every major market and are holding
- 1/3rd of restaurant food demand became takeaway as opposed to on-premise. When you change the logistic model you change the labor efficiency, rent efficiency, and the economics of it all
- McKinsey survey indicates that 93% of senior supply-chain executives from across industries & geographies plan to increase the level of resilience across their supply chain.
- Messaging, priority setting, and leadership will matter more than ever
About Catherine
Educated as an engineer, Catherine has dedicated her career to the logistics industry, serving
the last 20 years in top leadership positions.
Through a powerful combination of business insight, technical competency, and executive
leadership, her expertise helps clients achieve optimal success by addressing their global supply
chain challenges and strategic initiatives from both an executive and operational perspective.
You can reach Catherine at: ccooper@worldconnections.com
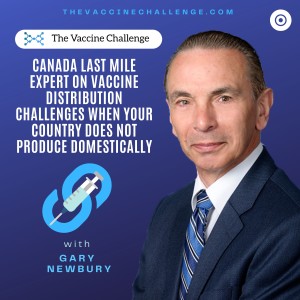
Thursday Mar 11, 2021
Thursday Mar 11, 2021
This episode of The Vaccine Challenge is hosted by Priyanka and features Gary Newbury - an Interim Executive and a Last Mile Expert in Canada.
2020 was all about the pandemic. 2021 is all about the COVID-19 vaccines.
With different pharma companies rolling out their respective vaccines consisting of various types of storage requirements, we talk to Gary about the developments in this space from a vaccine distribution perspective and what kind of challenges a country like Canada, where they have to completely rely on international production for their vaccine stocks, faces.
Topics touched upon:
What macro challenges does Canada face in terms of vaccine distribution:
-
The political angle of vaccine distribution and how “vaccine nationalism” is going to be a real thing. Economies can get restarted if the population is vaccinated and there’s a serious race to get there first
-
Population density in Canada is 3 people per square km - despite the fact that it is the second largest country in the world. England in comparison is 250 people per square km.
-
Also, Canada doesn’t have its own production capability which means it completely has to rely on international production which is subject to international logistics challenges too
-
Canada has a contract for 500 million vaccines signed up in Jan. The population of Canada is only 38mn. There’s a very political dimension to this whole situation and it's difficult to know how it’s all going to play out.
Where the biggest bottlenecks are:
-
The bottlenecks keep moving around. If there is production today, that might be a problem later. If there is good administration today, that might be a problem tomorrow.
-
Air freight capacity is really tight - because port congestion means other stuff is being put on flights. There is lesser crew availability too.
-
Can’t really line up and plan until the vaccine gets into Canadian soil. There is no way to guarantee that it WILL come as there is too much uncertainty. We can have right syringes PPE etc. but till you get the vaccines in hand, you can’t start putting plans in play.
-
What also ends up happening is that you use half vaccines, put the rest in the fridge to give the second doze to those that got the first doze because you cannot guarantee if the vaccines will come on time. So the number of people who can get vaccinated within a certain timeframe get cut in half.
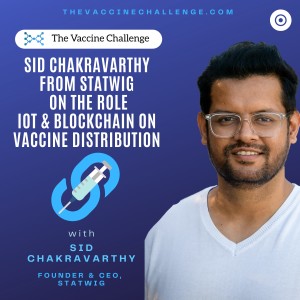
Thursday Mar 04, 2021
Thursday Mar 04, 2021
This episode of The Vaccine Challenge is hosted by Priyanka Asera and features Sid Chakravarthy, CEO & Founder of StaTwig. StaTwig leverages emerging technologies such as blockchain, Internet of Things and AI to create continuous visibility and complete traceability of every single vial of vaccine along its journey from a manufacturer to a beneficiary. Sid is UNICEF Innovation Fund Alumni, Gavi Infuse participant and World Economic Forum Global Innovator.
India is the land of vaccine development - with over 60% of the world vaccine manufacturing happening here. India has also had some very successful vaccination drives over the decades-- eg. with the elimination of polio - so it has a ready infrastructure. This gives developing countries like India, an edge over developed countries that haven’t had to deal with the number of vaccination drives common in developing and under-developed nations.
We talk to Sid about the role of emerging technologies in successful vaccine distribution and how it can help reduce waste.
Topics touched upon:
Lay of the land from a distribution perspective for vaccines and what StaTwig has been doing pre-pandemic:
- India is the largest manufacturer of vaccines world-over. 60% of global production happens in India. One-third is for domestic demand. Two-thirds are imported. Major distributors of vaccines are UNICEF, GAVI and local governments
- StaTwig started a Proof of Concept in early 2017. It is recognized by UNICEF & The World Economic Forum, and moves 2-3 bn doses of vaccines on its platform each year
- Supply Chain already has a lot of solutions - ERP, WMS, fleet management, OMS. But these are owned and controlled by separate stakeholders creating data silos and lack of visibility. StaTwig takes a more product-centric approach by creating a Digital ID. For eg. For each vial of vaccine in this case. Pharma industry’s regulation requiring the serialization of each vial helped in this effort
What are the biggest challenges StaTwig helps solve and how:
- Helps avoid and reduce cold chain failures - temperature excursions during storage and transportation of vaccines, as well as helps avoid expired and counterfeit products
- IoT has already become prominent. StaTwig links IoT data to individual vials of vaccine. Their platform acts like a record book. You type the serial number and they can tell you where it’s been and what the temp was at each point
- It can help identify if the product was mishandled, if there were temp problems in specific locations, it can ensure quality and safety of the product. It can also makes them regulatory compliant because a lot of governments are requiring track & trace
- VVM (Vaccine Vial Monitor) can tell you when a vaccine fails by changing color but you’ll only know that in the end when you open the shipment. StaTwig helps you track and know at the source in real time when the cold chain breaks down. When you can find out WHERE the cold chain breaks, you can preempt and avoid failures in the immediate future by making amends
- 1-2bn doses of COVID-19 vaccines expected to move through the StatWig platform this year. 25-30% failures can be avoided by the technology StaTwig leverages.
How do you track for inoculations and how does India fare when it comes to vaccine drives:
- Have a simple mobile-based wallet to track two-dose inoculations and send reminders to people. Unique ID of a vaccine is linked to a Unique ID of a person - this closes the loop
- In India, you register on the CoWIN app to schedule appointments through the app so the government can track vaccine coverage.
- Immunization camps are very successful in India generally because of the diseases they had to deal with and so the infrastructure already exists. Developed countries will see more issues in supply chain than developing or under-developed countries for that reason because governments and supply chains are used to such vaccine drives
About Sid
Sid Chakravarthy is Founder and CEO of StaTwig, which develops supply chain intelligence solutions such as VaccineLedger that ensures quality and safety of the vaccines in the extended supply chains. VaccineLedger leverages emerging technologies such as blockchain, Internet of Things and AI to create continuous visibility and complete traceability of every single vial of vaccine along its journey from a manufacturer to a beneficiary. Sid is UNICEF Innovation Fund Alumni, Gavi Infuse participant and World Economic Forum Global Innovator.
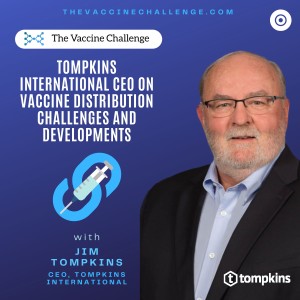
Thursday Feb 25, 2021
Jim Tompkins on Effect of the COVID19 Pandemic on Global Supply Chains of the Future
Thursday Feb 25, 2021
Thursday Feb 25, 2021
This episode of The Vaccine Challenge is hosted by Priyanka Asera and features Jim Tompkins, Founder and Chairman of Tompkins International. Jim has had four and a half decades of experience in the industry – and is an absolute legend in the space.
2020 was all about the pandemic. 2021 is all about the COVID-19 vaccines.
We change gears in this episode and talk to Jim about how the pandemic is going to affect global supply chains of the future.
Topics touched upon:
Lay of the land from a supply chain perspective due to the pandemic:
- Huge growth of eCommerce and BOPIS (Buy Online Pick-Up in Store) - 10 year jump ahead due to the pandemic
- Severe shift in demand patterns due to WFH which has totally disrupted global supply chains. Forecasting of demand was based on historicals past performance; now there’s no precedence.
What are the bottlenecks and challenges in vaccine distribution execution:
- Should we a) Maximize for the number of people that get the vaccine b) Slow the spread of COVID19, or c) Try to reduce the deaths from COVID 19. All these 3 strategies will significantly change what the Supply Chain strategy will be, and govts can’t seem to agree on what is best
- More important to know how many people were administered the vaccine rather than how many vaccines were distributed
- In many countries of the world, the cold chains are over-capacitated due to vaccines taking up cold chain capacity. Several countries have added new cold chain capacity just for the vaccine distribution and deployment.
Why is the old supply chain dead, and what does the new supply chain look like:
- “Black swan events” have been occuring more and more frequently. US Army in 1988 developed a term called VUCA - Volatility, Uncertainty, Complexity and Ambiguity. COVID19 ended up being the mother of all VUCAs. Regular supply chains cannot help deal with VUCA events.
- Earlier, it was a linear point-to-point supply chain which is too slow to deal with VUCA. It needs to be replaced with a real-time many-to-many communication that overcomes information latency so that everyone has the same version of the truth so we can respond to real time in VUCA.
- The answer is a Digital Supply Network. Requires a Control Tower over your entire ecosystem.
- One Network (leaders in control tower + AI +ML) have been doing a good job in this space
About Jim
- Dr. James A. Tompkins is an international authority on designing and implementing end-to-end supply chains. As the founder and Chairman of Tompkins International, his focus over the last several years has been in the areas of digital commerce, unichannel and supply chain reinvention. Over the last 40 years, Tompkins International has evolved from a supply chain consulting firm into an end-to-end supply chain consulting and solutions company, with business units focusing on supply chain consulting, material handling integration, and robotics. His 40-plus years as CEO of Tompkins International and his focus on helping companies achieve profitable growth give him an insider’s view into what makes great companies even better.
- Jim received the prestigious Frank and Lillian Gilbreth Industrial Engineering Award from the Institute of Industrial and Systems Engineers (IISE) on June 1, 2015. The award is an attribute that recognizes Dr. Tompkins through the contributions he has provided to the welfare of mankind in the field of industrial and systems engineering. In addition, Jim has served as President of the IISE, the Materials Management Society and the College-Industry Council on Material Handling Education and has been named a Distinguished Engineering Alum by Purdue University. He has also received more than 50 additional awards for his service to his profession.
- Jim is a thought leader, sharing insights on supply chain excellence through his thousands of presentations around the world and his YouTube videos have had over a million views. Jim also shares his knowledge and provides up-to-date information on supply chain and business trends via Linkedin and Twitter. He has written or contributed to more than 30 books and over 1,000 articles and has been quoted in hundreds of business and industry magazines.
- Jim received his Bachelor of Science in Industrial Engineering in 1969, his Master of Science in Industrial Engineering in 1970 and his Ph.D. in 1972, all from Purdue University.
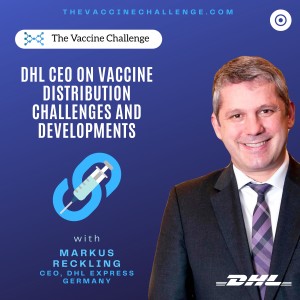
Thursday Feb 18, 2021
DHL Express Germany, CEO on Vaccine Distribution Challenges and Developments
Thursday Feb 18, 2021
Thursday Feb 18, 2021
This episode of The Vaccine Challenge is hosted by Priyanka Asera and features Markus Reckling, CEO of DHL Express, Germany. Markus has decades of experience in the industry – both in logistics and retail.
2020 was all about the pandemic. 2021 is all about the COVID-19 vaccines.
With different pharma companies rolling out their respective vaccines consisting of various types of storage requirements, we talk to Markus about the developments in this space from a vaccine distribution perspective and how DHL is contributing to this mega task.
Topics touched upon:
Lay of the land from a distribution perspective for the COVID-19 vaccines and what DHL is doing:
- Roughly 10bn dozes need to be shipped worldwide within 2021. This translates to 200,000 pallets, 15mn cooling boxes, 15000 flights across all flight chains and throughout the value chain
- After 12-24 months there will likely be a routine process, but up until then it’s all hands on deck
- Transportation material also doubles down as cooling and storage material where there are no cold storage capabilities – which is most clinics around the world – so the boxes in which vaccines are transported is also used as storage in hospitals and clinics
- Soon there will be there will be the challenge of too much vaccine going to spots that will be need to be dealt with
- DHL is already doing a lot of work in healthcare. Within their customer portfolio, they have 150 pharmacists, 20 clinical trial depots, 100+ certified stations, 160+ Good Distribution Practice (GDP) sites, 50+ Good Manufacturing Practice (GMP) sites, and can process medical shipments in 135+ medical sites globally. They deliver in 220+ countries and territories.
- The aim is to reach the 3bn in the less developed world also and not just the 5bn in the developed world
What are the cold chain challenges, restrictions and requirements
- Even the -80 Degree requirement for the Pfizer vaccines can last 10 days with dry ice packaging
- There are 3 types of cooling levels in logistics. Ambient is at 2-8 Degrees, typical deep frozen is at -20 Degree C, and -80 Degree C requirement is very limited and rare around the world
Biggest challenges around vaccines distribution
- Air freight capacity is limited. 50% of global air freight normally goes in passenger air crafts, and not dedicated cargo aircrafts. So 25% of global freight capacity is just missing because half the passenger airplanes are not flying.
- DHL has their own air freight capacity which puts them in a great position. Had ordered some new cargo aircrafts a few years ago - 6 new white body aircrafts B-777. Have bought 8 more B-777 recently for use in 2022.
- Availability of the crews in the right place, with all the lockdowns etc. Sometimes they have to fly empty planes to ensure pilots are in the right place. Also have to spend a fortune on disinfecting aircrafts
- Temp control and extreme temps requires a very coordinated effort. There’s only so much dry-ice you can put on an aircraft due to regulatory requirements. Need dedicated people at origin and destination who know what to do and avoid handling mistakes
- Security risks are huge because the commodity is so high value
Things that will likely change permanently in the world of supply chain as a result of COVID:
- Increase in certified stations and transportation providers in healthcare to prepare for more such scenarios in the future
- Investment in “Resilience”. Resilience is something that has been discussed just as a concept for the last 7-10 years. With all the struggles this time, it’ll be given much more importance and investment
- Continued boom in eCommerce: 30% more deliveries were seen in 2020 on peak day compared to peak day in 2019. That’s a fundamental shift which will keep increasing.
- B2C change will drive B2B change in eCom to a large extent. Small companies are also gearing for more connected, global supply chains. Alibaba’s of the world are driving this change rapidly.
About Markus
Markus Reckling is Managing Director, DHL Express Germany. He has worked for Deutsche Post DHL Group for more than 20 years in Germany and abroad. His prior positions included Head of Corporate Development, where he was responsible for developing Strategy 2015 and directly reported to the Group CEO, as well as the Managing Director of DHL Express Turkey. Currently, at DHL Express Germany Markus is responsible for the German business of the world's leading express service provider for international time-critical shipments with a focus on customer service, quality and employee motivation. Experienced in leadership and finding individual solutions for different tasks, Markus enjoys to share and discuss his learnings. Previously he worked for Otto Group and other German retailers. Combining his logistics experience with retail knowledge, Markus is a big promoter of eCommerce.
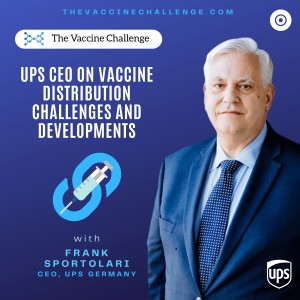
Sunday Feb 07, 2021
UPS Germany CEO on Vaccine Distribution Challenges and Developments
Sunday Feb 07, 2021
Sunday Feb 07, 2021
This episode of vaccine challenge hosted by Priyanka features Frank Sportolari, CEO of UPS Germany with 35 years of experience in the industry.
About Frank:
Frank Sportolari joined UPS in Munich, Germany in 1986 and held various positions of increasing responsibility in Germany, Spain, Italy and Brussels. In September 2011 he was appointed as President of UPS Germany.